Welding and fabricating are commonly used in equipment repair to restore the functionality and structural integrity of various types of machinery and tools. Whether it’s heavy machinery, industrial equipment, or even smaller tools, welding and fabrication techniques can be crucial in getting them back into operational condition. Here’s how welding and fabricating are involved in equipment repair:
1. Assessment and Diagnosis:
- The first step in equipment repair is to assess the extent of damage or malfunction. Engineers and technicians examine the equipment to identify the areas that require repair or replacement.
2. Welding Techniques:
- Different welding techniques are employed based on the type of equipment and the materials involved.
- Common welding processes, such as arc welding, TIG welding, MIG welding, and spot welding, are used to repair or replace damaged parts.
3. Fabrication of Replacement Parts:
- In cases where original parts are no longer available, or they are costly to replace, fabricating new parts is a cost-effective solution.
- Fabricators create custom components that match the specifications of the original parts.
4. Structural Repair:
- Welding is used to repair structural components of equipment, such as frames, chassis, brackets, and supports.
- Reinforcing weak or worn-out areas with additional metal helps restore the equipment’s strength.
5. Component Repair:
- Welding can be used to repair individual components, such as shafts, gears, hinges, and joints, by rejoining broken pieces or reinforcing weak points.
6. Alignment and Calibration:
- Welding and fabrication are often involved in aligning and calibrating parts of equipment to ensure proper functioning.
7. Weld Inspection:
- After welding, inspections are conducted to verify the quality of welds and ensure they meet industry standards.
- Non-destructive testing methods are used to detect potential defects.
8. Safety Considerations:
- Safety is a top priority in equipment repair involving welding and fabrication. Proper protective gear, ventilation, and safety protocols are followed to prevent accidents.
9. Finish and Protection:
- After welding and fabrication, finishing processes like grinding, painting, or coating may be applied to protect the repaired areas from corrosion.
10. Testing and Validation: – Repaired equipment is subjected to rigorous testing to ensure that it meets performance standards and functions as intended.
11. Documentation: – Detailed documentation of the repair process, materials used, welding procedures, and testing results is essential for future reference and compliance.
Here are some of the benefits of using welding to repair equipment:
- Welding is a strong and durable way to join metal parts together.
- Welding can be used to repair a wide range of equipment damage.
- Welding is a relatively quick and efficient way to repair equipment.
- Welding can be used to make equipment stronger and more durable.
Here are some of the challenges of using welding to repair equipment:
- Welding requires the expertise of a qualified welder.
- Welding can be a dangerous process if not done properly.
- Welding can produce fumes and other pollutants that can be harmful to the environment.
Overall, welding is a versatile and effective way to repair equipment damage. However, it is important to use a qualified welder and to take the necessary safety precautions when welding.
Here are some of the most common welding methods used for equipment repair:
- Arc welding: Arc welding is a process that uses an electric arc to melt the metal parts together. This is the most common welding method used for equipment repair.
- Gas welding: Gas welding uses a gas flame to heat the metal parts and then a filler rod is used to join the parts together. This method is often used for repairs that require a lot of flexibility.
- Resistance welding: Resistance welding uses heat from the resistance of the metal parts to melt them together. This method is often used for repairs that require a lot of speed and efficiency.
The best welding method for a particular equipment repair will depend on the type of damage, the materials being repaired, and the desired results.
Here are some of the safety precautions that should be taken when welding equipment:
- Wear appropriate personal protective equipment (PPE), such as a welding helmet, gloves, and goggles.
- Work in a well-ventilated area to avoid breathing in fumes.
- Use the correct welding method and materials for the job.
- Follow the manufacturer’s instructions for the equipment being repaired.
By following these safety precautions, you can help to prevent injuries and damage to equipment when welding.
Welding and fabricating play a vital role in extending the lifespan of equipment, reducing downtime, and maintaining operational efficiency. When equipment breaks down or experiences wear and tear, skilled welders and fabricators can help bring it back to optimal working condition, minimizing the need for costly replacements.
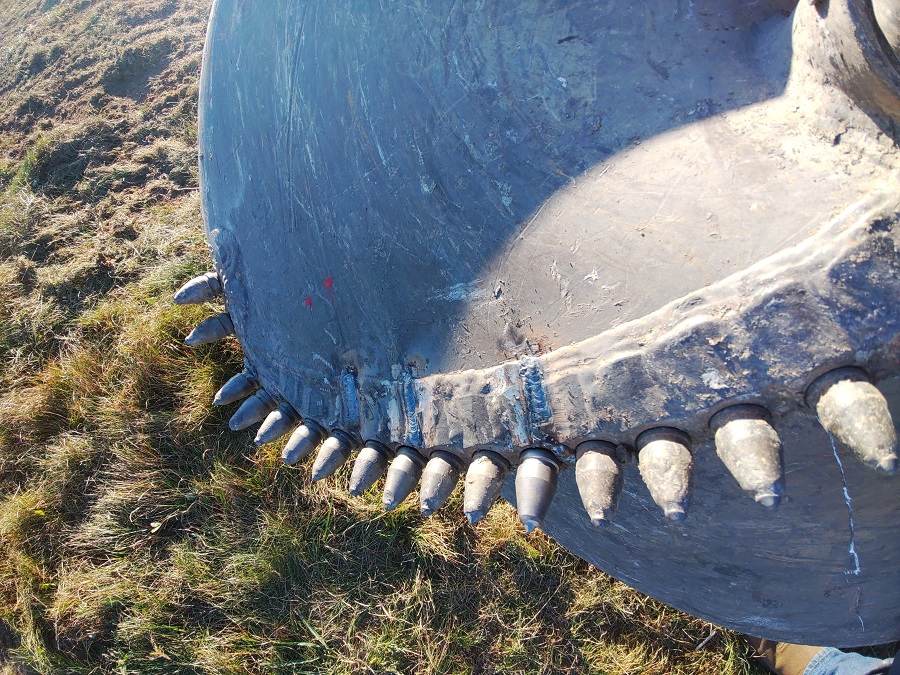